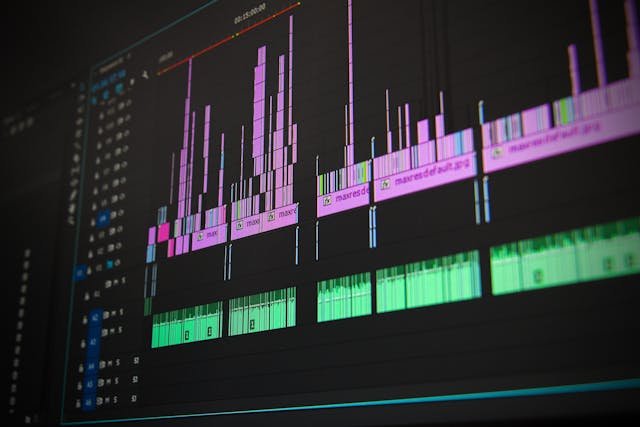
Maintaining equipment and ensuring smooth operations are critical for any business. A computerized maintenance management system (CMMS) plays a vital role in tracking, scheduling, and managing maintenance activities. Pairing this with failure mode and effects analysis (FMEA) can help predict and prevent equipment failures before they occur. This blog will explain how these tools can improve efficiency, reduce downtime, and enhance overall operations.
What is a CMMS?
A computerized maintenance management system is a software tool designed to manage maintenance tasks efficiently. It helps organizations track their equipment’s performance, schedule preventive maintenance, and record all service activities. With a CMMS in place, companies can extend equipment lifespan, reduce the risk of sudden breakdowns, and streamline operations.
Whether it’s a small business or a large corporation, CMMS helps eliminate manual maintenance logs, reducing human error and increasing productivity. It tracks everything from work orders to inventory management, making sure every detail is covered.
How Failure Mode and Effects Analysis (FMEA) Complements CMMS
While a CMMS helps with tracking and scheduling maintenance, failure mode and effects analysis (FMEA) focuses on identifying potential points of failure within your systems. FMEA helps businesses understand what can go wrong, how severe the failure could be, and what impact it might have on operations. This method prioritizes areas that need attention, ensuring that resources are directed where they are needed the most.
When FMEA is integrated into a CMMS, the combined effect is powerful. You get a proactive system that not only tracks and manages maintenance but also predicts potential failures, helping you avoid costly repairs or unscheduled downtime.
The Benefits of Using CMMS and FMEA Together
- Increased Equipment Lifespan Using both CMMS and FMEA helps predict when maintenance should be performed, thus avoiding unnecessary wear and tear. This prolongs the life of the equipment and reduces replacement costs.
- Reduced Unplanned Downtime Predictive maintenance enabled through FMEA, ensures that potential problems are addressed before they cause a breakdown. This reduces unplanned downtime, saving time and money.
- Improved Safety With a clear understanding of failure modes and their effects, businesses can ensure a safer work environment by addressing high-risk equipment and processes.
- Cost Efficiency Efficient maintenance schedules and proactive repairs mean that businesses can save on emergency repair costs. Investing in routine, preventive maintenance is always more cost-effective than handling large-scale failures.
- Better Resource Allocation By prioritizing potential failure points through FMEA, businesses can allocate their maintenance resources more effectively. Instead of performing maintenance on equipment that is in perfect condition, they can focus efforts where the risks are highest.
Key Features of a Good Computerized Maintenance Management System
- Work Order Management CMMS allows you to create, manage, and track work orders easily. It assigns tasks to specific team members and tracks their progress, ensuring timely completion of all tasks.
- Preventive Maintenance Scheduling With automated reminders, you never miss a maintenance schedule. This feature helps you reduce the likelihood of unexpected breakdowns by ensuring that equipment is maintained regularly.
- Asset Management CMMS stores detailed records of all assets, including their maintenance history, manuals, and warranty details. This ensures that all relevant data is accessible when needed.
- Inventory Management A good CMMS includes an inventory tracking feature, allowing you to monitor the availability of parts and supplies. This prevents delays in repairs due to missing components.
- Reporting and Analytics Detailed reports give you insights into your maintenance operations, helping you make data-driven decisions. You can track metrics like the mean time between failures (MTBF) and the mean time to repair (MTTR) to optimize your processes.
How FMEA Improves Maintenance Planning
When you conduct an FMEA, you identify potential failure points and their impact on your operations. This helps in creating a more targeted maintenance plan. For example, if a specific machine is more prone to failure, FMEA highlights that risk. With this information, you can schedule more frequent inspections or maintenance for that machine through your CMMS.
FMEA also provides insights into the severity of potential failures. By understanding which failures would have the most significant impact, you can prioritize repairs and ensure that critical equipment is always functioning correctly.
Real-World Application
Imagine a manufacturing plant using a computerized maintenance management system (CMMS) to manage its maintenance operations. The system tracks all machines, schedules preventive maintenance, and manages spare parts inventory. However, the plant still experiences unexpected breakdowns. By integrating FMEA, the plant can analyze the reasons behind these failures, identifying which machines are most likely to fail and why. Armed with this knowledge, the plant adjusts its maintenance schedule, focusing more on high-risk equipment. This not only reduces downtime but also boosts productivity and safety.
Conclusion
Combining a CMMS with failure mode and effects analysis (FMEA) is an effective way to enhance your maintenance strategy. While CMMS handles the day-to-day tracking and scheduling, FMEA helps predict and prevent failures before they occur. This proactive approach to maintenance can save businesses time, money, and resources in the long run.
Optimize your maintenance strategy today with Micromain’s computerized maintenance management system (CMMS). Book a free demo and discover the power of smart maintenance management.